با پیشگیری از هزینه های خوردگی، هر دوسال می توان یک پالایشگاه ساخت!
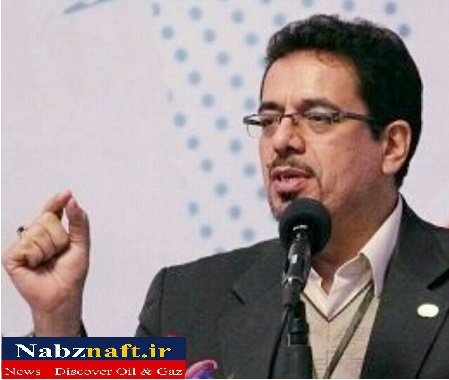
ابزار و روش
یافته های ارائه شده در این مقاله در خصوص مقایسه روش تعمیر کامپوزیتی با دو روش رایج تعویض بخش آسیب دیده لوله یا اسلیوگذاری یا غلاف بندی بیرونی و جوش، حاصل تجربیات آزمایشگاهی و میدانی طی 3-4 سال اخیر می باشد.
فناوری تعمیر خوردگی و تقویت کلاس خطوط، با دانش فنی بومی و داخلی، بیش از 3 سال است که در حال معرفی این فناوری به صنایع نفت و گاز است و موفق به اخذ تایید بازرسی فنی شرکت ملی گاز ایران و ورود به وندور لیست شرکتهای خطوط انتقال گاز ایران و خطوط لوله و مخابرات نفت شده است. این فناوری خوشبختانه در چند سال اخیر در ایران بصورت متعدد تست میدانی و همچنین بصورت پروژه های اجرایی وسیع، عملیاتی شده است. همچنین برای نشر دانش این فناوری، بصورت سخنرانی کلیدی یا مقالات، در کنفرانس های علمی خوردگی، خطوط انتقال و HSE ارائه شده است. در آینده نزدیک، شاهد استفاده گسترده و ملی از این فناوری در کشورمان خواهیم بود.
این روش باوجود داشتن مزایای ایمنی، سهولت، سرعت و دوام و ماندگاری که در بخش بعدی ارائه خواهد شد، دارای مزیت صرفه جویی قابل توجه در هزینه ها نسبت به روش سنتی است اما با این وجود درکشور ما چندان عملیاتی نشده و سالهاست که در سطح پروژه تحقیقاتی باقی مانده است اما طی چند سال اخیر، توجه بیشتر و جدی تری نسبت به آن شده است. ارائه آمار و مقایسه هزینهها به استناد ارگانهای تحقیقات داخلی و شرکتهای معتبر خارجی، ضرورت توجه هر چه سریعتر به منظور عملیاتی شدن و جایگزینی این روش را تایید مینماید.
کاربردهای متنوع فناوری "پوشش های کامپوزیتی پیشرفته" برای خطوط انتقال نفت و گاز و همچنین مخازن (مورد استفاده و رایج در صنایع حساس و high tech هوایی و دریایی کشور) مطابق استانداردهای جهانی:
1- تعمیر خوردگی و درز و ترک و حتی سوراخ های ریز ایجاد شده در خطوط انتقال و مخازن
2- پیشگیری از خوردگی حتی در بدترین شرایط آب و هوایی و خاک و حتی خطوط عبوری از دریا
3- پیشگیری از آسیب با زلزله های خفیف و رایج در کشور بدلیل انعطاف آنها.
4- پیشگیری از نشتی خطوط انتقال گاز و فراورده های نفتی و کمک به برنامه ها و تعهدات کاهش انتشار کربن
5- تقویت کلاس یعنی افزایش ظرفیت واقعی خطوط انتقال (استفاده از ظرفیت کامل خطوط آسیب دیده در حال بهره برداری و یا استفاده بالاتر از ظرفیت خط در خطوط آسیب ندیده یا جدید) بجای ایجاد خط جدید یا مکمل خط موجود.
همزمان با افزایش کاربرد کامپوزیت در خطوط لوله، تولید لوله های کامپوزیتی برای انتقال فرآورده های نفت و گاز، با شرایط خاص و حساس مورد نیاز، مورد توجه قرار گرفته و در دنیا حتی برای حساس ترین خطوط دریایی تولید میشود و در ایران نیز در مرحله تحقیق و توسعه است و آینده خوبی برای این خدمت، صنعت و محصول پیش بینی می شود. لوله های کامپوزیتی سه مزیت مهم دارند: از نسبت مقاومت به وزن بالایی برخوردارند، انعطاف پذیری بالایی دارند و فاقد خورندگی هستند. این لوله ها به صورت پیوسته و بر روی قرقره تحویل می شوند. امکان تولید این لوله ها با طول نامحدود وجود دارد و می توان از آنها در آب های عمیق نیز بهره برد. آزمایش های انجام شده در مورد اتصال دو رشته خط لوله زیردریایی با یک فلنج نیز موفقیت آمیز بوده است.[8]
با برطرف شدن چالش های اولیه، به نظر می رسد لوله های کامپوزیتی از آینده ای درخشان برخوردار باشند. از سوی دیگر، قیمت ارزان این محصول، برگ برنده دیگر فناوری کامپوزیت محسوب می شود[8].
یافته ها
بر اساس تست ها و تجربیات میدانی متعدد، در ادامه، مزیتهای روش تعمیر و تقویت خطوط انتقال فراورده های نفت و گاز با "پوشش های نانو کامپوزیتی پیشرفته" نسبت به روش های سنتی جاری ارائه گردیده اند. همچنین در جدول شماره 1 ویزگی ها و مزیت های روش مورد تاکید، با دو روش سنتی یعنی اسلیوگذاری یا برش و تعویض قسمت آسیب دیده لوله، در مواردی که امکان اجرای آن وجود دارد، مقایسه نیز شده اند.
مزایای تعمیر با روش کامپوزیتی نسبت به روش سنتی [6,7]:
1- قابلیت اجرای پوشش و انجام تعمیر، حین بهره برداری از خط، لذا عدم نیاز به قطع و خارج کردن خط از سرویس
2- قابلیت اجرا در طول لوله و fitting ها. حتی در لوله هایی که بیش از 85% از ضخامت خود را از دست دادهاند.
3- قابليت بازگرداندن لولههاي خورده شده به وضعيت اوليه طراحي
4- امکان تقویت فلنج و سرجوشهای آسیب دیده ناشی از زلزله
5- افزایش مقاومت خط انتقال در برابر زلزله
6- جلوگیری از خوردگي لوله در آينده پس از تعمیرات و درنتیجه عمر مفید بالا
7- ایمنی بالاتر و کاهش حوادث با حذف برش و جوشكاري
8- حذف هزینه های فرصت از دست رفته ناشی از قطع خط
9- عدم نیاز به تخلیه خط و در نتیجه جلوگیری از هدررفت سوخت در محیط
10- حذف هزینه های مربوط به تعویض خط
11- سهولت و سرعت اجرا: وزن كم مواد كامپوزيت و عدم نیازبه تجهیزات وسیع و ماشین آلات، باعث سهولت نصب آنها میشود. تعمير به وسيلة دو نفر بدون نياز به لوازم و دستگاه هاي ويژه انجام ميشود.کل زمان مورد نیاز برای انجام پوشش جهت تعمیر هر مقطع، حدود 2 ساعت است.
12- حذف تبعات بالای اقتصادی، سیاسی و اجتماعی ناشی از قطع جریان خط
13- تطابق کامل با محیط زیست بعد از نصب
14- قابل استفاده در تمام شرایط جوی، جغرافیایی و شرایط سیال حامل
15- هزینه کمتر تعمیر
تقویت لوله، تقویت کلاس خط و افزایش ظرفیت انتقال- نیاز روز صنعت نفت:
با توجه به افزایش ظرفیت تولید و برداشت گاز از پارس جنوبی و میادین مشترک، یکی از دغدغه های اصلی که طی چند ماه گذشته و حتی زمستان سال قبل (بعد از قطع گاز از طرف ترکمنستان) مطرح شد، اختلاف ظرفیت اسمی و ظرفیت واقعی خطوط انتقال است.
حتی همان زمان اینگونه مطرح شد که تولید یا برداشت گاز داریم اما بسرعت امکان انتقال نداریم چون همزمان با افزایش ظرفیت تولید، ظرفیت انتقال گاز به مناطق مختلف کشور (برای مصارف مختلف) ایجاد نشده است.
دو راهکار وجود دارد:
الف: ایجاد خطوط انتقال جدید در کنار خطوط قبلی: این راهکار، بسیار هزینه بر و زمان بر است. علاوه بر این، در برخی مناطق از جمله مناطق شمالی در زمین های کشاورزی، محدودیت زمین هم وجود دارد که ممکن است این گزینه را غیرممکن سازد.
ب: تقویت خطوط انتقال موجود با پوشش کامپوزیت پیشرفته بصورت سراسری با هدف استفاده از حداکثر ظرفیت اسمی خط. حتی بهره بردرای بالاتر از ظرفیت اسمی بعد از انجام پوشش کامپویتی تست شده و موفقیت آمیز بوده است، اما حتی استفاده از کل ظرفیت اسمی خطوط یک هدف عالی در صنعت نفت محسوب می شود.
تخمین زده می شود که بصورت خوشبینانه متوسط ظرفیت در حال بهره برداری خطوط، 80% ظرفیت اسمی آن است. در برخی خطوط که لوله های بکاررفته اشکال اساسی در متریال داشته اند، روی 60% ظرفیت در حال بهره برداری هستند. با همین ظرفیت بهره برداری هم نشت و انتشار نفت و گاز وجود دارد.
اگر همان 80% خوشبینانه را ظرفیت واقعی بهره برداری از خطوط قلمداد کنیم، بدون ایجاد خط جدید، با پوشش خطوط انتقال اصلی با کامپوزیت پیشرفته نانویی، ظرفیت انتقال را تا 25% وضع فعلی می تواند افزایش دهد که موفقیت بزرگی برای صنعت نفت و گاز کشور خواهد بود.
مزیت های زیست محیطی پوشش های تقویتی و تعمیراتی کامپوزیتی:
فناوری پوشش های نانوکامپوزیتی پیشرفته در خطوط انتقال گاز، نفت و فرآورده های نفتی، از مزیت های زیست محیطی زیر بروردار است:
1- کاهش انتشار کربن در خطوط در حال بهره برداری، قبل از نیاز به تعمیر (در راستای برنامه ها و تعهدات):
میزان نشت یا هدر رفت سالیانه گاز در خطوط انتقال گاز کشور، حدود 10 میلیارد متر مکعب اعلام شده است (تقریبا معادل کل صادرات ایران به ترکیه). با پوشش کامپوزیتی خطوط، از بخش قابل توجهی از این حجم انتشار و هدررفت گاز، پیشگیری میشود.
حسب اطلاع، در مجموعه برنامه های شرکت ملی گاز ایران و شرکت خطوط انتقال گاز ایران، یکی از طرح های مصوب برای کاهش انتشار، همین راهکار پوشش های کامپوزیتی است.
در نتیجه، فناوری پیشنهادی، در همین حوزه، جدای از مزیت زیست محیطی، مزیت اقتصادی قابل توجهی هم دارد. (ارزش حجم گازی که از هدررفت آن جلوگیری می شود)
2- جلوگیری از انتشار نفت، بنزیین و دیگر فراورده های نفتی در کلیه خطوط انتقال کشور و کمک به محیط زیست و پیشگیری از زیان ها و تخریب های زیست محیطی.
3- عدم نیاز به تخلیه گاز یا فرآورده های نفتی خط در طبیعت حتی در صورت نیاز به تعمیر خوردگی. این مزیت به سلامت و حفظ محیط زیست، کمک می کند.
جدول 1: مزیت تعمیر خطوط لوله با روش نانو کامپوزیت در مقایسه با برش لوله و تعویض و اسیلوگذاری[6,7]
ردیف |
فاکتورهای مقایسه روشهای تعمیر خوردگی |
برش لوله و تعویض |
اسلیوگذاری sleeve (نصب و جوشکاری) |
اعمال کامپوزیت |
1 |
نیاز به قطع خط- خارج کردن از سرویس |
دارد |
دارد |
ندارد |
2 |
نیاز به تخلیه خط- تخریب محیط زیست |
دارد |
دارد |
ندارد |
3 |
زمان انجام تعمیر |
زیاد |
زیاد |
کم |
4 |
تجهیزات سنگین برای انجام تعمیرات |
دارد |
دارد |
ندارد |
5 |
تعداد نیروی کار و سطح مهارت مورد نیاز |
زیاد- خیلی مهم |
کمتر- متوسط |
خیلی کم- محدود |
6 |
جوشکاری و محدودیت های عملیاتی |
دارد |
دارد |
ندارد |
7 |
ریسک ایمنی کار گرم |
دارد |
دارد |
ندارد |
8 |
تنشهای وارده به لوله ناشی از جوشکاری |
دارد |
دارد |
ندارد |
9 |
نیاز به پوشش مجدد لوله |
دارد |
دارد |
ندارد |
10 |
خوردگی های مجدد (بیرونی) |
وابسته به پوشش |
وابسته به پوشش |
ندارد |
11 |
افزایش عمر خط لوله |
متوسط |
کمتر |
طولانی |
12 |
هزینه |
زیاد |
متوسط |
کم |
نتيجه گيري[6,7]
به جای روشهای برش و تعویض و یا جوشکاری غلاف فلزی بر روی لوله جهت تعمیر خوردگی و تقویت کلاس خطوط لوله های تحت فشار نفت وگاز، پوشش نوین نانو کامپوزیت پیشرفته ی اپوکسی/ الیاف شیشه به همراه پرایمر و چسب های قوی ساختاری با خواص منحصر بفرد و پرایمر ضد خوردگی، برای تعمیر نواحی اسیب دیده لوله خورده شده مطابق ضوابط تعیین شده طبق استانداردهای مربوطه، به دلیل مزایای خوبی همچون: زمان کم فرایند تعمیر، قیمت مناسب، تدارکات و نفرات بسیار کمتر، عدم قطع و توقف جریان نفت وگاز، حذف احتمال حوادثی مانند انفجار و آتش سوزی، عدم نیاز به پوشش مجدد لوله ترمیمی و ... بعنوان یک راهکار نوین، مطمئن، ایمن و مقرون بصرفه توصیه میشود.
حسب تجربه 3-4 ساله، مهمترین چالش امروز، نیاز به آموزش های گسترده فنی تخصصی جهت آشنایی مدیران و کارشناسان بخش های مهندسی خوردگی و بازرسی مجموعه های شرکتها و صنایع نفت، گاز و پتروشمی کشور، اعتماد آنها به مستندات، تجارب میدانی موجود و تاییدیه های معتبر و تشویق آنها به استقبال آنها از فناوری روز می باشد. یک دغدغه هم، تاکید بیشتر کارفرمایان بر فاکتور یا معیار هزینه در انتخاب شرکتها و پیمانکاران مجری این روش است که لازمست از هم سطح بودن و قابل قیاس بودن مشخصات فنی نوع و کیفیت تعمیر شرکتها از نظر معیارها و شاخصهای اصلی، حصوص اطمینان شود و الزامات استانداردی ملاک تعیین تعداد لایه ها یا ضخامت پوشش کامپوزیتی باشد نه هزینه تعمیر. چون، ارائه جدول مشخصات فنی مواد و متریال مصرفی، رعایت الزامات استانداردی، حساسیت در انتخاب متریال بویژه ترکیب چسبهای سازه ای خاص و تعیین تعداد لایه های پوشش بر اساس استاندارد و مطابق با شرایط، نیاز و ریسک خط لوله، از اهمیت بسیار بالایی برخوردار است.
سپاسگزاری
از آقای دکتر مهدی زونیا مدیرعامل محترم شرکت سپاهان پلیمر فام، بابت انتقال تجارب علمی و فنی و همچنین همکاری در انجام مطالعات مربوط به این مقاله، سپاس گزاری میکنم.
منابع و ماخذ
1- مجموعه مقالات دومین همایش خوردگی در صنعت نفت: خسارات ناشی از خوردگی در ایران و جهان
(پایگاه خبری صنعت بازرسی، 1 تیر 90)
http://www.migmag.ir/index.php/1390-03-08-14-10-37/1390-04-18-18-14-03/66-corossion
2- مصاحبه 25 آبان 95 مهندس علیرضا عربی اصل، مدير كل راهبري نظام نگهداري و تعميرات صنعت نفت در نشست خبري كنگره خوردگي، به نقل از خبرنگار شانا
http://www.ecofars.com
www.shana.ir
3- خبر 25 آبان 94 خبرگزاری ایلنا، گزارش نشست خبری سومین کنگره خوردگی صنعت نفت، مصاحبه جابر نشاطی رئیس انجمن خوردگی ایران
http://www.ilna.ir/fa/tiny/news-322398
4- خبر 5 مهر 94 سایت پترومی (petrome.ir) : مصاحبه مهندس عباسعلی جعفری نسب مدیرعامل شرکت خطوط لوله و مخابرات نفت ایران
http://petrome.ir/1394/07/05/001274.php
5- خبر 15 مهر 96 سایت شرکت خطوط انتقال گاز ایران: مصاحبه مهندس محمد کارخانه معاونت خطوط لوله شرکت انتقال گاز ایران
6- مجموعه مقالات دومین همایش پوشش خطوط لوله- آیان 94: تعمیر خوردگیو تقویت کلاس خطوط لوله های گاز توسط فناوری کامپوزیت پیشرفته (مهدی زونیا، حسین سلیمانی، سیدکاظم بحرینی)
http://iranpipelines.com/fa
7- مقاله یا یادداشت 24 آذر 95 سایت عصر نفت (asrenaft.com) : برای پیشگری از چالش های خطوط لوله چه باید کرد؟ آدرس به پوشش های کامپوزیتی پیشرفته- 24 آذر 95- نویسنده دکتر جواد نوفرستی
8- مقاله یا یادداشت 22 آبان 95 سایت عصر نفت (asrenaft.com) : کامپوزیت؛ میهمان جدید صنعت نفت- نویسنده: جان شیهان، مترجم: محسن داوری، منبع www.epmag.com